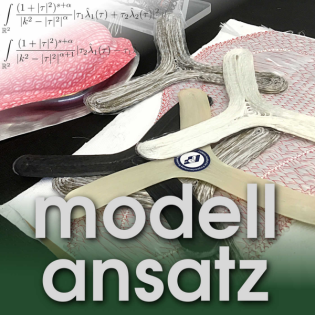
Podcast
Podcaster
Beschreibung
vor 5 Jahren
Gudrun war in Dresden zu Gast am Leibniz Institut für
Polymerforschung. Sie spricht dort mit Axel Spickenheuer und Lars
Bittrich über deren Forschungsfeld, das
Tailored-Fiber-Placement-Verfahren (TFP). Anlass des Treffens in
Dresden war der Beginn einer gemeinsamen Masterarbeit.
Das Institut für Polymerforschung hat - zusammen mit
Vorgängerinstitutionen - eine längere Geschichte in Dresden. Seit
1950 gab es dort ein Institut für Technologie der Fasern (als
Teil der Akademie der Wissenschaften der DDR). Dieses wurde 1984
zum Institut für Technolgie der Polymere und nach der Gründung
des Freistaates Sachsen schließlich am 1.1. 1992 neu als Institut
für Polymerforschung Dresden e.V. gegründet. Seitdem wird dort
auch schon an der TFP-Technologie gearbeitet. Seit 2004 gehört
das Institut der Leibniz-Gemeinschaft an. Es ist damit der
anwendungsnahen Grundlagenforschung verpflichtet.
Ein wichtiges Thema im Haus ist Leichtbauforschung. Die
TFP-Verfahren beinhalten Verstärkung von Geweben oder
Thermoplasten durch feste Fasern aus z.B. Glas, Kohlenstoff und
Aramiden. Diese Verstärkung kann man so aufbringen, dass sie in
allen Richtungen gleich stark wirkt (isotrop) oder aber so, dass
sich sehr unterschiedliche Materialeigenschaften bei
Beanspruchung in unterschiedlichen Richtungen ergeben
(anisotrop).
In den so entstehenden zusammengesetzten Materialien geht es
darum, für die Bauteile Masse zu reduzieren, aber Steifigkeit
und/oder Tragfähigkeit stark zu erhöhen. Besonderes Potential für
Einsparungen hat die anisotrope Verstärkung, also die (teuren)
Fasern genau so zu einzusetzen, wie es den berechneten
Anforderungen von Bauteilen am besten entspricht. Das führt auf
sehr unterschiedliche Fragen, die in der Forschungstätigkeit des
Dresdner Instituts beantwortet werden. Sie betreffen u.a. die
tatsächliche Herstellung an konkreten Maschinen, die
Kommunikation zwischen Planung und Maschine, die Optimierung des
Faserverlaufs im Vorfeld und die Prüfung der physikalischen
Eigenschaften.
Die Verstärkungsstruktur wird durch das Aufnähen einzelner
sogenannter Rovings auf dem Basismaterial erzeugt. Das
Grundmaterial kann eine textile Flächenstruktur (Glasgewebe,
Carbongewebe, Multiaxialgelege) oder für thermoplastische
Verstärkungsstrukturen ein vernähfähiges Folienmaterial sein. Die
Verstärkungsstrukturen werden durch die Bewegung des
Grundmaterials mit Hilfe einer CNC-Steuerung und der
gleichzeitigen Fixierung des Rovings mit Hilfe des Nähkopfes
gefertigt. Um eine hohe Effektivität zu erhalten, können
Verstärkungsstrukturen mit bis zu 1000 Stichen pro Minute
hergestellt werden.
Für die Mathematik besonders interessant ist die Simulation und
Optimierung der sehr komplexen Verbundstoffe. Um optimale
Faseranordnungen umsetzen zu können, braucht es natürlich
numerische Methoden und prozessorientierte Software, die
möglichst alle Schritte der Planung und Herstellung
automatisiert. Traditionell wurde oft die Natur zum Vorbild
genommen, um optimale Verstärkungen - vor allem an Verzweigungen
- nachzuahmen. Hier gibt es einen Verbindung nach Karlsruhe ans
KIT, denn Claus Mattheck hat hier über viele Jahrzehnte als
Leiter der Abteilung Biomechanik im Forschungszentrum Karlsruhe
richtungsweisend gearbeitet und auch mit dem Institut für
Polymerforschung kooperiert.
Ein weiterer Ansatz, um gute Faserverläufe zu konstruieren ist
es, die Hauptspannungsverläufe (insbesondere 1. und 2.
Hauptspannung) zu berechnen und das Material entsprechend zu
verstärken. Dies ist aber für die komplexen Materialien gar nicht
fundiert möglich.
Eine der derzeit wichtigsten Problemstellung dabei ist die
hinreichend genaue Modellbildung für eine Finite Elemente Analyse
(FEA). Erst dadurch lassen sich exakte Vorhersagen zum späteren
Bauteilverhalten bzgl. Steifigkeits- und Festigkeitsverhalten
treffen. Besonders schwierig sind dabei
die Berücksichtigung der lokal variablen Dicken im FE-Modell
bzw. die genaue Wiedergabe der lokalen Faserorientierung darin.
Vorzeigebeispiele für die Leistungsfähigkeit der Technologie sind
die Fenster des Airbus und ein sehr leichtgewichtiger Hocker
(650g), der bis zu 200 kg Last tragen kann und auch noch schick
aussieht. Er wurde inzwischen in vielen technischen Ausstellungen
gezeigt, z.B. im Deutschen Museum München.
Mit Hilfe der am Institut entwickelten Softwaretools EDOPunch und
AOPS (nach der Kommerzialisierung wurden daraus die Produkte
EDOpath und EDOstructure der Complex Fiber Structures GmbH) ist
es nun möglich, ausgehend von einem nahezu beliebigen
TFP-Stickmuster, 3D-FEA-Simulationsmodelle zu erstellen, die in
einem makroskopischen Maßstab sowohl die lokale Dickenkontur
(sozusagen den Querschnitt) als auch die lokale Faserorientierung
entsprechend abbilden können. Erste Ergebnisse zeigen, dass sich
hierdurch sehr gut das Steifigkeitsverhalten solcher
variabelaxialer Faserverbundbauteile berechnen lässt. Neben dem
Vorgehen zum Erstellen entsprechender Simulationsmodelle wird
anhand verschiedener experimentell ermittelter Bauteilkennwerte
die Leistungsfähigkeit des verwendeten Modellansatzes immer
wieder demonstriert.
Die Weiterentwicklung dieser Software geht über die Ziele des
Instituts für Polymerforschung hinaus und wird seit März 2013 in
der Ausgründung Complex Fiber Structures erledigt. Ziel ist es,
allen Ingenieuren die mit Faserverbünden arbeiten, sehr einfach
handhabbare Tools zur Planung und Entwicklung zur Verfügung
stellen zu können. Es gibt hierfür sehr unterschiedliche typische
Nutzungsfälle. Im Gespräch geht es z.B. darum, dass Löcher in
klassischen Bauteilen regelmäßig zu starken Festigkeitseinbußen
führen. Allerdings kann man sehr oft nicht auf Löcher im Bauteil
verzichten. TFP-Lösungen können aber so umgesetzt werden, dass im
Verbundmaterial die Festigkeitseinbuße durch Löcher nicht mehr
vorhanden ist. Damit Ingenieure diesen Vorteil für sich nutzen
können, brauchen sie aber gute Software, die ihnen solche
Standardprobleme schnell zu lösen hilft, ohne sich erst in den
ganzen Hintergrund einzuarbeiten.
Axel Spickenheuer hat Luft-und Raumfahrttechnik an der TU Dresden
studiert und arbeitet seit 2005 am Institut für Polymerforschung.
Seit vielen Jahren leitet er die Gruppe für Komplexe
Strukturkomponenten und hat 2014 zum Thema TFP-Verfahren
promoviert.
Lars Bittrich hat an der TU Dresden Physik studiert und zu
Quantenchaos promoviert. Dabei hat er schon viel mit numerischen
Verfahren gearbeitet. Seit Ende 2010 ist er Mitglieder von Axels
Gruppe.
Literatur und weiterführende Informationen
L. Bittrich e.a.: Buckling optimization of composite
cylinders for axial compression: A design methodology considering
a variable-axial fiber layout more. Composite Structures 222
(2019) ID110928
L. Bittrich e.a.: Optimizing variable-axial fiber-reinforced
composite laminates: The direct fiber path optimization concept
more. Mathematical Problems in Engineering (2019) ID 8260563
A. Spickenheuer: Zur fertigungsgerechten Auslegung von
Faser-Kunststoff-Verbundbauteilen für den extremen Leichtbau auf
Basis des variabelaxialen Fadenablageverfahrens Tailored Fiber
Placement Promotionsschrift TU Dresden, 2014.
Podcasts
H. Benner, G. Thäter: Formoptimierung, Gespräch im
Modellansatz Podcast, Folge 212, Fakultät für Mathematik,
Karlsruher Institut für Technologie (KIT), 2019.
M. An, G. Thäter: Topologieoptimierung, Gespräch im
Modellansatz Podcast, Folge 125, Fakultät für Mathematik,
Karlsruher Institut für Technologie (KIT), 2017.
A. Rick, S. Ritterbusch: Bézier Stabwerke, Gespräch im
Modellansatz Podcast, Folge 141, Fakultät für Mathematik,
Karlsruher Institut für Technologie (KIT), 2017.
P. Allinger, N. Stockelkamp, G. Thäter: Strukturoptimierung,
Gespräch im Modellansatz Podcast, Folge 053, Fakultät für
Mathematik, Karlsruher Institut für Technologie (KIT), 2015.
Weitere Episoden

16 Minuten
vor 10 Monaten

1 Stunde 42 Minuten
vor 1 Jahr

50 Minuten
vor 2 Jahren

42 Minuten
vor 2 Jahren

35 Minuten
vor 2 Jahren
In Podcasts werben
Abonnenten

Neutraubing

Darmstadt

Groß Gusborn
Kommentare (0)