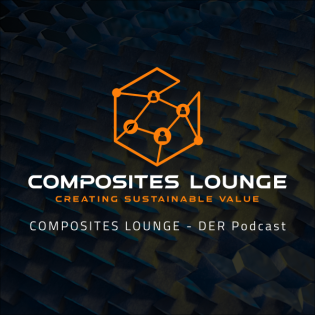
#138 Examining with Dr. Phil Gralla on how "Hardware in the Loop" significantly increases data analysis
40 Minuten
Podcast
Podcaster
Der Podcast mit Praxiswissen aus dem Bereich der Faserverbundwerkstoffproduktion und Anwendung
Beschreibung
vor 4 Monaten
Welcome to our two part episode where Composites Lounge invited
Dr Dr. Phil Gralla of sensXPERT - Optimizing Plastics
Manufacturing to explain how "Hardware in the Loop" (HIL)
increases data analysis.
Ilkay Özkisaoglu found this a fascinating way to utilize data and
if you are not familiar with HIL and how your manufacturing of
plastics and composites can benefit from it, listen to this
episode.
sensXPERT opened its doors end of April 2024 and it took a while
to compile this live demo, because we wanted to create the best
possible experience, know-how transfer and you to understand the
practice of AI, more precisely ML applied to inmold plastics and
composites components.
There are also some developments that are contactless, since
requirements in trenchless technologies assume a test from a
certain distance after installation.
A little more background on HIL to warm you up on this particular
episodes, because these are truly technical:
What is hardware-in-the-loop (HIL)?
According to MathWorks.com "HIL (Hardware-in-the-loop) simulation
is a technique for validating your control algorithm to be run on
a specific target controller by creating a real-time virtual
environment that represents the physical system to be controlled.
HIL allows you to test the behavior of your control algorithms
without physical prototypes.
How does HIL simulation work?
You create and simulate a real-time virtual implementation of
physical components—such as a production plant with sensors and
actuators—on a target computer.
You run the control algorithm on an embedded controller and run
the model of the plant or environment in real time on a target
computer connected to the controller. The embedded controller
interacts with the plant model simulation through multiple I/O
channels.
You refine software representations of your components and
gradually replace parts of the system environment with the actual
hardware components.
With this approach, HIL simulation can avoid expensive iterations
in hardware manufacturing.
Where are HIL simulations used?
HIL simulations are particularly useful when testing your control
algorithm on the real physical system would be expensive or
dangerous. HIL simulations are commonly used in automotive,
aerospace and defense, industrial automation and engineering to
test embedded designs.
Examples of commonly used HIL simulations include:
Aerospace and defense: flight simulators and flight dynamics
control where it would be too complex to test the control
algorithm on the actual aircraft
Automotive: vehicle dynamics and control where it would not make
sense to test functionality in the early stages on the road
Industrial automation: plant control testing when stopping
production or assembly lines to test control algorithms would
mean high resource costs and business losses" (Mathworks.com
online accessed 23 Aug 2024, Link in the comments)
Weitere Episoden

3 Minuten
vor 1 Monat

1 Stunde 17 Minuten
vor 1 Monat

6 Minuten
vor 2 Monaten

15 Minuten
vor 2 Monaten

11 Minuten
vor 2 Monaten
In Podcasts werben
Kommentare (0)